In 2019, the global composites market reached a volume of 17.7 megatons, valued at $86 billion. The markets in China (28%) and North America (26%) remain the largest in terms of volume, ahead of Europe (21%) and the rest of Asia (19%).
According to the JEC Observer study, the fiberglass market accounted for approximately 90% of composite production volume in 2020. However, carbon fiber-reinforced polymer (CFRP) materials are increasingly used across a wide range of applications, including in the aerospace, land, and maritime transportation sectors, wind turbines, hydrogen storage tanks, and sports equipment. Economically, CFRPs represent more than 25% of the composites market due to the high production cost of carbon fibers.
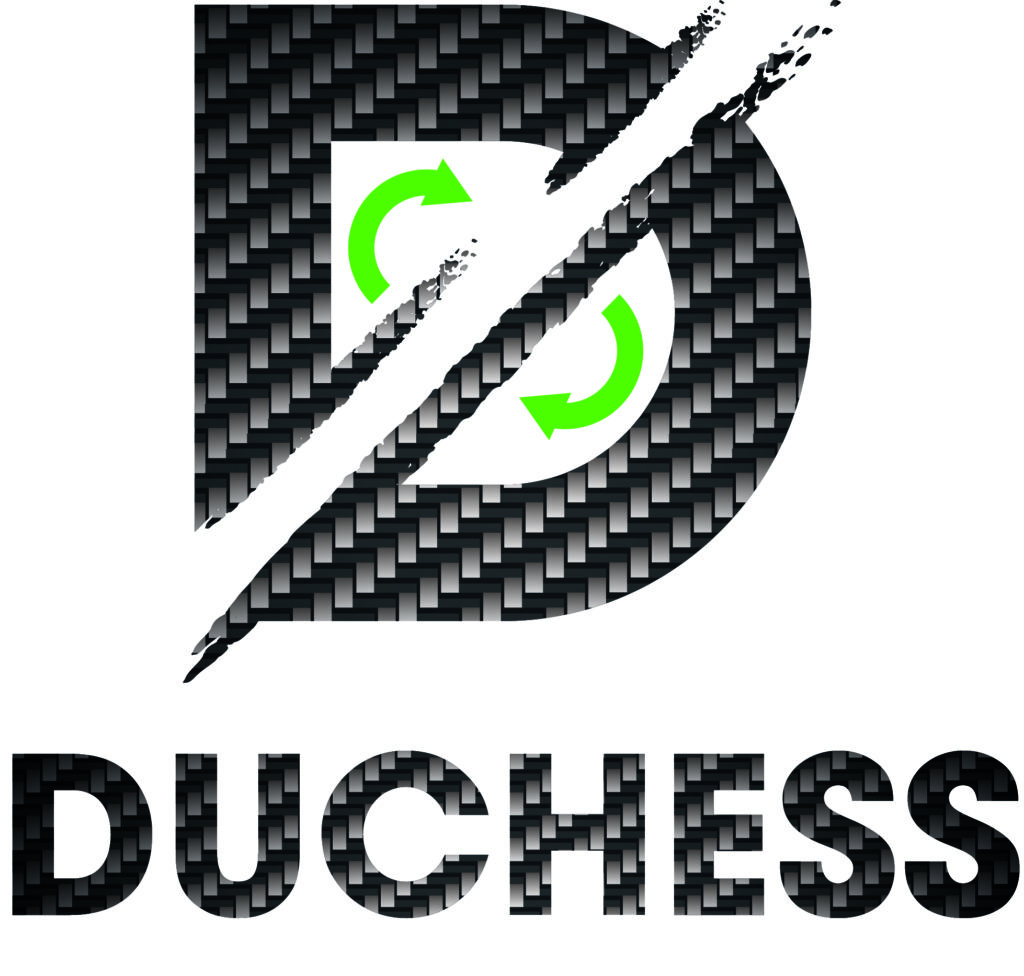
This growing demand for CFRPs is primarily due to their high mechanical properties, low density, ease of integrating multiple functions into the final part, and design flexibility. Notably, global CFRP demand tripled between 2010 and 2020 and is expected to exceed 300,000 tons per year by 2030 (Figure 1). The significant increase in carbon fiber demand also places considerable pressure on producers, whose production capacity may not suffice to meet the demand.
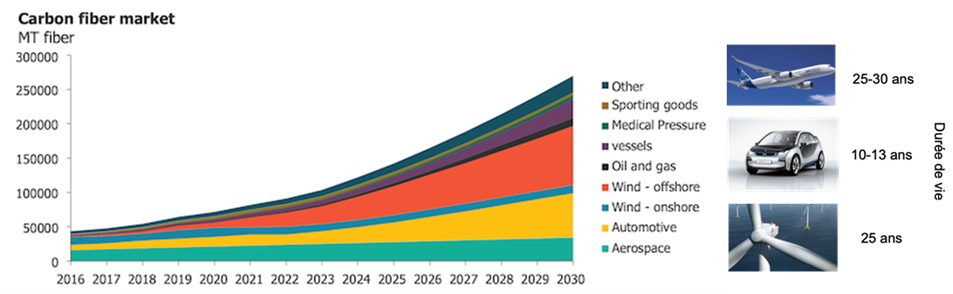
Figure 1: Evolution of the carbon fiber market and lifespan of composite parts by application
These increases inevitably lead to a rise in the amount of materials reaching end-of-life. In the wind energy and aerospace industries, certain studies have estimated that waste volumes related to these sectors will grow rapidly, reaching nearly 1 million tons of CFRP waste generated worldwide by 2050. Therefore, it becomes essential to create an industrial ecosystem capable of valorizing this waste and generating added value, rather than bearing the cost of its disposal.
Recycling and reprocessing recycled carbon fibers (rCF) require approximately 10 to 30% of the energy needed to produce virgin carbon fibers.
Processes for valorizing recycled carbon fibers are beginning to emerge at the industrial scale, notably the vapothermolysis process, which preserves surface condition and mechanical properties up to about 95% compared to virgin fibers.
The DUCHESS project aims to adapt and demonstrate innovative industrial-scale processes for reprocessing recycled carbon fibers into oriented fibers in the form of continuous yarn spools and mats. These products will open up a range of semi-structural applications for rCFs that currently do not exist in the French market at a commercial scale, aligning with a complete circular economy approach.
In this context, the main objectives of the DUCHESS project are:
- Specify the technical characteristics of rCF yarn spools and mats to ensure perfect compatibility with existing textile processing methods.
- Produce rCFs from waste sources using the vapothermolysis process.
- Optimize and produce semi-finished products such as non-wovens, tapes, and rovings from rCFs.
- Optimize and produce rCF yarn spools compatible with the targeted application (in accordance with point 1).
- Adapt existing industrial textile processes (weaving, braiding, TFP, etc.) for processing continuous rCF yarns and mats to produce and test technical textiles based on rCFs.
- Additionally, the DUCHESS project aims to demonstrate a high level of product competitiveness, ensuring that production costs are compatible with industrial scaling for the targeted market application.
This project was funded by the French State as part of France 2030 operated by ADEME.
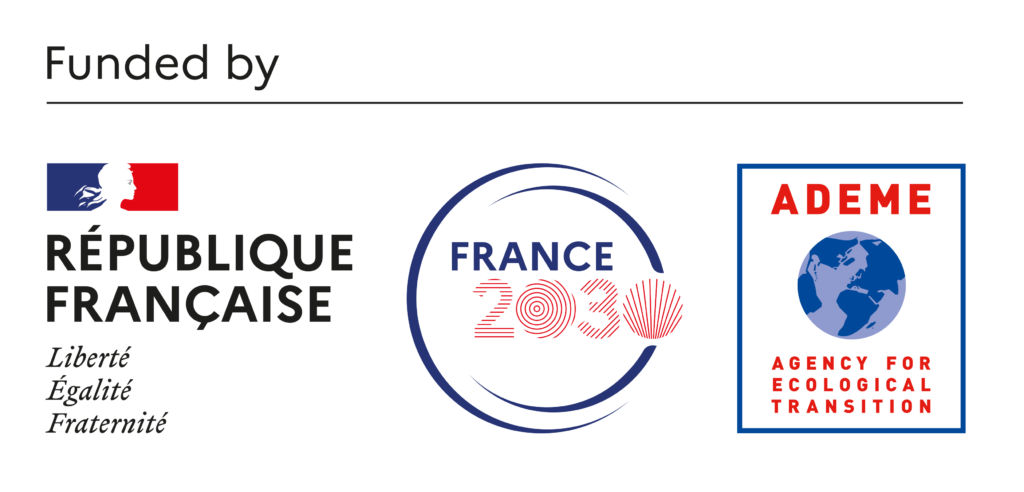
References:
[1] JEC. JEC Observer: Overview of the Global Composites Market 2019-2024 2020.
[2] Das S, Warren J, West D, Laboratory ORN. Global Carbon Fiber Composites Supply Chain Competitiveness Analysis. Technical Report 2016.
[3] GREC – Guide du Recyclage et de l’Ecoconception des Composites. La librairie ADEME n.d. https://librairie.ademe.fr/dechets-economie-circulaire/5577-grec-guide-du-recyclage-et-de-l-ecoconception-des-composites.html (accessed April 3, 2023).
[4] CFRP Market at $64 Billion by 2030. PlasticstodayCom 2020. https://www.plasticstoday.com/composites/cfrp-market-64-billion-2030.
[5] The future of carbon fiber manufacture 2022. https://www.compositesworld.com/articles/the-future-of-carbon-fiber-manufacture.
[6] Lefeuvre A, Garnier S, Jacquemin L, Pillain B, Sonnemann G. Anticipating in-use stocks of carbon fiber reinforced polymers and related waste flows generated by the commercial aeronautical sector until 2050. Resources, Conservation and Recycling 2017;125:264–72. https://doi.org/10.1016/j.resconrec.2017.06.023.
[7] Zhang J, Chevali VS, Wang H, Wang C-H. Current status of carbon fibre and carbon fibre composites recycling. Composites Part B: Engineering 2020;193:108053. https://doi.org/10.1016/j.compositesb.2020.108053.
[8] Jiang J, Deng G, Chen X, Gao X, Guo Q, Xu C, et al. On the successful chemical recycling of carbon fiber/epoxy resin composites under the mild condition. Composites Science and Technology 2017;151:243–51. https://doi.org/10.1016/j.compscitech.2017.08.007.